LW EFOLIT
EFOLIT® Taped High Frequency Litz Wires
General
The EFOLIT product family represents a triple insulated taped litz wire design with VDE-certification for reinforced insulation, which is necessary to certify products for high voltage applications. Litz wire diameters up to 5.0 mm with temperature class F/155°C and H/180°C cover a wide range of operating temperatures for various power applications.
According to specification:
DIN EN 62368, annex J
DIN EN 61558, annex K
DIN EN 60601, annex L
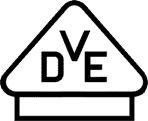
Features and benefits of EFOLIT® - litz wires
Technical properties of EFOLIT® - litz wires
Operating range
Winding wires for reinforced insulation | |
---|---|
Max. rated and peak voltage | 1000 Vrms 1414 Vpeak |
Max. frequency | 500 kHz |
Temperature class | F / 155 °C H / 180 °C |
Technical data of taping material
Self-adhesive tape | sPET | sPEN |
---|---|---|
Description | Polyester | Polyethylene Naphtalate |
Permittivity (JIS C 2318) | 3.2 | 2.9 |
Tape - UL file no. | E 515235 | E 515235 |
Processing | Fusible | Fusible |
Product identification
Validated standards | Code | sPET | sPEN |
---|---|---|---|
IEC/DIN EN 61558, 60950, 62368, 60601 VDE-Reg. no. E078 (nom. test voltage: 6 kV) |
EFOLIT 11F | Class F with enamel type TI = 155°C / 311°F |
- |
EFOLIT 22H | - | Class H with enamel type TI = 180°C / 356°F |
|
IEC/DIN EN 60950, 62368 VDE-Reg. no. E450 (nom. test voltage: 3 kV) |
EFOLIT 13F * | Class F with enamel type TI = 155°C / 311°F |
- |
EFOLIT 24H * | - | Class H with enamel type TI = 180°C / 356°F |
TI = Temperature Index
* Also certified as basic insulation acc. IEC/DIN EN 61558, Annex K
Dimensional range
Diameter single conductor | 0.030 - 0.300 mm 48 - 28 AWG |
Total conductor cross section | 0.100 - 10.600 mm2 |
Outer diameter litz wire (approx.) | 0.500 - 5.000 mm 24 - 4 AWG |
Tape insulation (min.) | 3 layers |
Applications
- EV (Electric Vehicles)
- OBC (Onboard charger)
- DC/DC converter
- Wireless charging
- Charging piles
- SMPS (Switch Mode Power Supplies)
- HF transformers
- HF transducers
- HF chokes
Litz Wire Details
Litz Wire
Single Wire Diameter vs Range of Frequency
range of frequency [kHz] | dominal diameter of single wire [mm] | ||
---|---|---|---|
from | to | from | to |
0.06 | 1 | 0.4 | 0.254 |
1 | 10 | 0.254 | 0.2 |
10 | 20 | 0.2 | 0.127 |
20 | 50 | 0.127 | 0.102 |
50 | 100 | 0.102 | 0.079 |
100 | 200 | 0.079 | 0.063 |
200 | 350 | 0.063 | 0.05 |
350 | 850 | 0.05 | 0.04 |
850 | 1400 | 0.04 | 0.03 |
1400 | 3000 | 0.03 | 0.02 |
Influence of Litz Wire Parameters on Litz Wire Freatures
construction parameters | |||||||||
---|---|---|---|---|---|---|---|---|---|
conductor material | nom. diameter single wire ØSW | no. of single wires nSW | no. of bundles & bunching steps | length of lay SL per bunching step | pitch direction SR per bunching step | thickness of enamelling | |||
litz wire features | electrical | total cross section litz wire AConductor,Litz; direct current resistance RDC | X | X | X | ||||
high frequency resistance RAC; RF-losses | X | X | X | X | |||||
current density J = I/AConductor,Litz | X | X | |||||||
filling factor litz wire AConductor,Litz/Atot,Litz | X | X | X | X | X | ||||
breakdown voltage UBDV | X | ||||||||
mechanical (AConductor,Litz = const.) | outer diameter ODLitz;total cross section litz wire Atot,Litz | X | X | X | X | X | X | X | |
dimensional stability | X | X | X | X | X | ||||
flexibility | X | X | X | X | |||||
flexlife performance | X | X | X | X | |||||
max. tensile strength | X | ||||||||
surface structure, roundness | X | X | X | X | X |
Main influencing parameters for HF-coils
construction parameters | |||||||
---|---|---|---|---|---|---|---|
nom. diameter single wire ØSW | number single wires nSW | number bundles & bunching steps | length of lay SL per bunching step | pitch direction SR per bunching step | |||
litz wire features | electrical | total conductor cross section AConductor,Litz; direct current resistance RDC | X | X | |||
resistance at high frequency RAC; RF-losses | X | X | X | ||||
mechanical | outer diameter litz wire OD Litz; total cross section litz wire Atot,Litz | X | X | X | X | X | |
flexibiliy | X | X | X | X |
Optional Litz Constructions and Features
litz wire | construction | pitch direction SR | length of lay SL [mm] | bunching factor VF | features |
---|---|---|---|---|---|
270 x 0.071 mm | (54 x 0.071 mm) x 3 | S,S | 20;26 | ≈ 15 | good RF-performance, rough textured three-sided litz wire profile |
((30 x 0.071 mm) x 3) x 3 | S,S,S | 20;26;26 | ≈ 20 | good RF-performance, compact bunching | |
((18 x 0.071 mm) x 3) x 5 | S,S,S | 20;26;26 | ≈ 20 | good RF-performance, compact bunching, evenly surface and litz wire profile | |
((18 x 0.071 mm) x 3) x 5 | S,S,Z | 20;20;26 | ≈ 15 | fine litz wire structure/-surface | |
(39 x 0.071 mm) x 7; concen. | S+Z,S | 20+20;24 | < 13 | very round, dimensional stable litze wire profile, high flexibily |
Litz Wire Design for HF Coil with Specific Winding Window
practise-related approach | ||||
---|---|---|---|---|
frequency [kHz] | 50 | 125 | 200 | |
total no. of windings NW,tot | 30 | 30 | 30 | |
no. of layers NL (winding layers) | 3 | 3 | 3 | |
no. of windings per layer NW,L | 10 | 10 | 10 | |
outer diam. litz wire (grade 1) ODLitz [mm] |
with servg. | 2.19 | 2.19 | 2.19 |
without servg. | 2.32 | 2.32 | 2.32 | |
nom. diameter single wire ØSW [mm] |
0.100 | 0.080 | 0.063 | |
filling factor litz wire FillLitz [%] |
with servg. | 48.2 | 47.7 | 46.1 |
without servg. | 47.0 | 46.5 | 44.9 | |
filling factor winding window FillWind [%] |
with servg. | 25.9 | 26.3 | 24.9 |
without servg. | 29.1 | 29.2 | 27.2 | |
typ. litz wire construction |
with servg. | 225 x 0.100 mm 5x(45x0.100mm) |
360 x 0.080 mm 5x(4x(18x0.080mm)) |
550 x 0.063 mm 5x(5x(22x0.063mm)) |
without servg. | 255 x 0.100 mm 5x(51x0.100mm) |
400 x 0.080 mm 5x(4x(20x0.080mm)) |
600 x 0.063 mm 5x(5x(24x0.063mm)) |
Comparison of The Design Approaches
practise-related approach | approach acc. Ch. R. Sullivan | |||||
---|---|---|---|---|---|---|
frequency [kHz] | 50 | 125 | 200 | 50 | 125 | 200 |
total no. of windings NW,tot |
30 | 30 | 30 | 30 | 30 | 30 |
no. of layers NL (layer winding) | 3 | 3 | 3 | 3 | 3 | 3 |
no. of winding per layer NW,L |
10 | 10 | 10 | 10 | 10 | 10 |
outer diameter litz wire (grade 1) ODLitz [mm] |
2.19 | 2.19 | 2.19 | 2.17 | 2.18 | 2.19 |
nom. diameter litz wire ØSW [mm] |
0.100 | 0.080 | 0.063 | 0.071 | 0.050 | 0.040 |
filling factor litz wire FillLitz [%] |
48.2 | 47.7 | 46.1 | 46.9 | 46.1 | 45.2 |
filling factor winding window FillWin [%] |
25.9 | 26.3 | 24.9 | 25.3 | 25.0 | 24.6 |
typ. litz wire construction | 225 x 0.100 mm 5x(45x0.100mm) | 360 x 0.080 mm 5x(4x(18x0.080mm)) | 550 x 0.063 mm 5x(5x(22x0.063mm)) | 440 x 0.071 mm 5x(4x(22x0.071mm) | 875 x 0.050 mm 5x(5x(35x0.050mm)) | 1350 x 0.040 mm 5x(5x(54x0.040mm)) |
LW Spools
Spool and Packaging for Litz Wire
Spool Types
Spool Types | Diagramm | Wire Sizes | Characteristics | |
---|---|---|---|---|
Biconical | 1 | 37 - 58 AWG | 0.010 mm - 0.114 mm | Biconical spool for fine and ultrafine wire, superb de-reeling capability, ideal for high speed winding machines |
Cylindrical | 2 | 31 - 50 AWG | 0.050 mm - 0.511 mm | Straight barrel spool, solid traditional design |
Tapered | 3 | 24 - 38 AWG | 0.102 mm - 0.511 mm | Stable winding due to tapered barrel spool for heavier sizes |
Container | Container for large spools |
European Spools
Spool Type | d1 [mm] |
d4 [mm] |
I1 [mm] |
I2 [mm] |
Spool weight [g] |
Filling weight unserved litz wire* [kg] | Filling weight served & taped litz wire* [kg] | Filling weight extruded litz wire* [kg] | Spools per box | Spools per pallet max |
---|---|---|---|---|---|---|---|---|---|---|
125K | 125 | 16 | 125 | 100 | 200 | 2.0 | 1.3 | ** | 4/6/9 | 216 |
160K | 160 | 22 | 160 | 128 | 350 | 4.8 | 3.2 | 2.0 | 4 | 96 |
200K | 200 | 22 | 200 | 160 | 600 | 8.9 | 5.9 | 3.9 | 2 | 42 |
250K | 250 | 22 | 200 | 160 | 1050 | 16.6 | 11.0 | 7.3 | 1 | 36 |
355K | 355 | 36 | 200 | 160 | 1850 | 32.4 | - | ** | - | 12 |
VMV630 | 630 | 56 | 475 | 361 | 18500 | 214.0 | 178.0 | ** | - | 1 |
VM 710 | 710 | 52 | 250 | 180 | 18000 | - | 81.0 (taped) | ** | - | 4 |
400/56-275 | 400 | 56 | 275 | 241 | 4590 | 81.0 | 67.5 (taped) | ** | - | 4 |
Dimensions of the spool
d1 ➡ Flange Diameter
d4 ➡ Core diameter
l1 ➡ Overall width
l2 ➡ Traverse
* Approximate values valid for copper, for other metals please inquire.
** The extrusion machines only work with spools bore diameter of 22 mm / 0.87 inch.
Other packages on demand.
American Spools
Spool Type |
Flange diameter d1 [inch] |
Bore diameter d4 [inch] |
Overall width I1 [inch] |
Traverse length I2 [inch] |
Spool weight [lbs] |
Filling weight unserved litz wire* [lbs] |
Filling weight served & taped litz wire* [lbs] |
Filling weight extruded litz wire* [lbs] |
Spools per box max. | Boxes per pallet max. |
---|---|---|---|---|---|---|---|---|---|---|
3x3" | 3.15 | 0.63 | 3.15 | 2.52 | 0.16 | 1.23 | 0.82 | ** | 24 | N/A |
4x4" | 3.94 | 0.63 | 3.94 | 3.15 | 0.28 | 2.21 | 1.43 | ** | 6 | N/A |
5x5" | 4.92 | 0.63 | 4.92 | 3.94 | 0.54 | 4.41 | 2.87 | ** | 6 | 216 |
6x4" | 6.00 | 0.63 | 4.33 | 4.32 | 0.75 | 7.06 | 4.63 | ** | 6 | 125 |
6x6" | 6.30 | 0.87 | 6.30 | 5.04 | 0.8 | 10.58 | 7.06 | 4.85 | 4 | 96 |
8x8" | 7.87 | 0.87 | 7.87 | 6.30 | 1.35 | 19.62 | 13.01 | 8.60 | 2 | 42 |
250K | 9.84 | 3.01 | 7.80 | 6.22 | 3 | N/A | N/A | N/A | 1 | 36 |
355K | 13.98 | 1.42 | 7.87 | 6.30 | 4 | 71.44 | 59.54 | ** | N/A | 12 |
Spool Type |
Flange diameter d1 [mm] |
Bore diamter d4 [mm] |
Overall width I1 [mm] |
Traverse length I2 [mm] |
Spool weight [kg] |
Filling weight unserved litz wire* [kg] |
Filling weight served & taped litz wire* [kg] |
Filling weight extruded litz wire* [kg] |
Spools per box max. | Boxes per pallet max. |
---|---|---|---|---|---|---|---|---|---|---|
3x3" | 80 | 16 | 80 | 64 | 0.07 | 0.56 | 0.37 | ** | 24 | N/A |
4x4" | 100 | 16 | 100 | 80 | 0.125 | 1.00 | 0.65 | ** | 6 | N/A |
5x5" | 125 | 16 | 125 | 100 | 0.245 | 2.00 | 1.30 | ** | 6 | 216 |
6x4" | 152.4 | 16 | 110 | 109.7 | 0.340 | 3.20 | 2.10 | ** | 6 | 125 |
6x6" | 160 | 22 | 160 | 128 | 0.35 | 4.80 | 3.20 | 2.20 | 4 | 96 |
8x8" | 200 | 22 | 200 | 160 | 0.6 | 8.90 | 5.90 | 3.90 | 2 | 42 |
250K | 250 | 76.5 | 198 | 158 | 1.461 | N/A | N/A | N/A | 1 | 36 |
355K | 355 | 36 | 200 | 160 | 1.85 | 32.40 | 27.00 | ** | N/A | 12 |
Dimensions of the spool
d1 ➡ Flange Diameter
d4 ➡ Core diameter
l1 ➡ Overall width
l2 ➡ Traverse
* Approximate values valid for copper, for other metals please inquire.
** The extrusion machines only work with spools bore diameter of 22 mm / 0.87 inch.
Other packages on demand.
Asian Spools
Spool Type | d1 (mm) | d4 (mm) | l1 (mm) | l2 (mm) | d14 (mm) | Spool Weight (g) | Filling Weight unserved litz wire* (Kg) | Spools per box | Boxes per pallet max |
---|---|---|---|---|---|---|---|---|---|
PT-4 | 124 | 22 | 200 | 170 | 140 | 270 | 6 | 4 | 24 |
PT-10 | 160 | 22 | 230 | 200 | 180 | 620/420 | 12 | 2 | 30/40 |
PT-15 | 180 | 22 | 230 | 200 | 200 | 550 | 18 | 1 | 45/36 |
PT-25 | 215 | 32 | 280 | 250 | 230 | 1000 | 28 | 1 | 24 |
P-30 | 300 | 30 | 160 | 130 | 300 | 1230 | 20 | 1 | 24 |
K200C | 200 | 22 | 200 | 160 | 200 | 625 | 8 | 2 | 24 |
Dimensions of the spool
d1 ➡ Flange Diameter
d4 ➡ Core diameter
d14 ➡ Flange diameter
l1 ➡ Overall width
l2 ➡ Traverse
LW Determination of Winding Tension
Litz Wire
Determination of Winding Tension on Litz Wire
The following table shows the maximum applicable winding tension on the single litz wire strands. The maximum feasible winding tension for litz wires can be calculated by multiplying the number of single strands by the appropriate winding tension of the single strand. Regardless of this calculation, for litz wire diameters thicker than 5 mm tension limits of (420N) for hard metals and (270N) for copper and soft metals are recommended.
These values are guidelines and can deviate significantly depending on the manufacturing process.
Cu, Cu/Ag | |||
---|---|---|---|
[mm] | AWG | nom. [cN] | ± 20 % [cN] |
0.018 | 53 | 1.6 | 0.3 |
0.019 | 52.5 | 1.7 | 0.3 |
0.020 | 52 | 1.9 | 0.4 |
0.021 | 51.5 | 2.1 | 0.4 |
0.022 | 51 | 2.3 | 0.5 |
0.023 | 50.5 | 2.5 | 0.5 |
0.024 | 50.5 | 2.6 | 0.5 |
0.025 | 50 | 2.9 | 0.6 |
0.026 | 50 | 3.1 | 0.6 |
0.027 | 49.5 | 3.3 | 0.7 |
0.028 | 49 | 3.5 | 0.7 |
0.030 | 48.5 | 4.0 | 0.8 |
0.032 | 48 | 4.5 | 0.9 |
0.035 | 47 | 5.4 | 1.1 |
0.036 | 47 | 5.7 | 1.1 |
0.040 | 46 | 70.0 | 1.4 |
0.045 | 45 | 8.8 | 1.8 |
0.050 | 44 | 10.9 | 2.2 |
0.056 | 43 | 12.4 | 2.5 |
0.060 | 42.5 | 14.3 | 2.9 |
0.063 | 42 | 15.7 | 3.1 |
0.071 | 41 | 19.8 | 4.0 |
0.080 | 40 | 24.9 | 5.0 |
0.090 | 39 | 31.1 | 6.2 |
0.100 | 38 | 38.0 | 8.0 |
0.112 | 37 | 47.0 | 9.0 |
0.120 | 36.5 | 53.0 | 11.0 |
0.130 | 36 | 62.0 | 12.0 |
0.140 | 35 | 71.0 | 14.0 |
0.150 | 34.5 | 80.0 | 16.0 |
0.160 | 34 | 91.0 | 18.0 |
0.170 | 33.5 | 101.0 | 20.0 |
0.180 | 33 | 113.0 | 23.0 |
0.190 | 32.5 | 125.0 | 25.0 |
0.200 | 32 | 137.0 | 27.0 |
0.210 | 31.5 | 150.0 | 30.0 |
0.220 | 31 | 164.0 | 33.0 |
0.230 | 30.5 | 178.0 | 36.0 |
0.240 | 30.5 | 193.0 | 39.0 |
0.250 | 30 | 209.0 | 42.0 |
0.260 | 30 | 225.0 | 45.0 |
0.270 | 29.5 | 241.0 | 48.0 |
0.280 | 29 | 259.0 | 52.0 |
0.290 | 29.5 | 276.0 | 55.0 |
0.300 | 28.5 | 295.0 | 59.0 |
0.310 | 28 | 314.0 | 63.0 |
0.320 | 28 | 333.0 | 67.0 |
0.330 | 27.5 | 353.0 | 71.0 |
0.340 | 27.5 | 374.0 | 75.0 |
0.350 | 27 | 395.0 | 79.0 |
0.360 | 27 | 417.0 | 83.0 |
0.370 | 26.5 | 439.0 | 88.0 |
0.380 | 26.5 | 462.0 | 92.0 |
0.390 | 26 | 486.0 | 97.0 |
0.400 | 26 | 510.0 | 102.0 |
0.420 | 25.5 | 560.0 | 112.0 |
0.430 | 25.5 | 586.0 | 117.0 |
0.450 | 25 | 639.0 | 128.0 |
0.470 | 24.5 | 695.0 | 139.0 |
0.480 | 24.5 | 724.0 | 145.0 |
0.500 | 24 | 783.0 | 157.0 |
LW Connection Technologies
Litzwire
Connection Technologies for Litz Wires
Due to the many stranded nature of litz wires, terminating them often poses a challenge. The following table advises the connection technologies which are generally applicable for various insulations. Only the most important factors of influence have been classified. Many others, such as enamel type and insulation thickness of the single strands, heat resistance of the additional insulation, the stranding construction (tight/compact or wide/flexible), have not been addressed.
Litz wires without additional insulation | Litz wires with additional insulation | ||||||
---|---|---|---|---|---|---|---|
overall diameter < 1.0 mm | overall diameter ≥ 1.0 mm | Serving | Extrusion | Taping | |||
Connection technology | many fine single strands* | few heavy strands** | many fine single strands* | few heavy strands** | |||
Soldering | dip/flow/hand/wave soldering | dip/flow/hand/wave soldering | dip/flow soldering | dip/flow soldering | dip/flow soldering | dip/flow soldering | dip/flow soldering |
Mechanical skinning | -- | brushing | -- | brushing | taking off serving, brushing if necessary | stripping off coating, brushing if necessary | off/opening the tape, brushing if necessary |
Crimping (pre-stripped) | possible | possible | possible | possible | possible | possible | possible |
- welding - thermocompression - resistance - ultrasonic sound |
thermo-compression, ultrasonic sound | thermo-compression, ultrasonic sound, resistance | thermo-compression | thermo-compression, ultrasonic sound, resistance | Thermocompression (nylon) | thermocompression | mechanical removal of additional insulation recommended |
* nom. diameter ≤ 0,100 mm
** nom. diameter > 0,100 mm
Please contact us if the conductor metals are alloys.
Please contact us directly for futher assistance.
LW Abbreviations
Abbreviations
Abbreviations | ||
AConductor,Litz | = | total conductor cross section of litz wire |
Ages,Litz | = | total cross section of litz wire |
ODLitz | = | outer diameter of litz wire |
ODBundle | = | outer diameter of bundle |
nsw | = | number of single wires |
Øsw | = | nominal diameter of single wire |
VF | = | bunching factor |
SL | = | length of lay (bunching length) |
SR | = | pitch (bunching) direction |
RDC | = | DC resistance |
RAC | = | AC resistance |
f | = | frequency |
ρ | = | specific resistance of conductor |
µO | = | permeability of free space |
δ | = | skin depth |
J | = | current density |
UBDV | = | breakdown voltage |
b | = | width of winding window |
h | = | height of winding window |
NW,tot | = | total number of windings |
NL | = | number of winding layers |
NW,L | = | number windings per layer |
FillLitz | = | copper filling factor of litz wire |
FillWin | = | copper filling factor of winding window |
ne | = | recommended total number of single wires |
n1,max | = | number of single wires of basic bundle in 1st bunching step |
k | = | constant according Ch. R. Sullivan |
LW Smartbond
Smartbond Litz Wire
General
Products for multimedia applications are increasingly equipped with wireless charging devices. ELEKTRISOLA's Smartbond OSP18 has been developed to meet the needs of these specific charging systems. This self-bonding litz wire combines excellent bond strength with good windability, fast soldering, and very good hot air bonding characteristics.
The hot air bonding process is environmentally friendly compared to solvent bonding process, allows faster winding, and has potential for process automation. Very thin coils can be produced with Smartbond`s unique construction giving additional space for designers or to help to achieve miniaturization goals.
Features and benefits of Smartbond litz wires
- excellent bonding strengths with hot air bonding
- high winding speed
- solderable without pre-stripping of insulation
- environmentally friendly automated process due to elimination of solvents
- thin walled overcoat allows small coils
- customized wall thickness possible per customer specification
Technical properties of Smartbond litz wire
Standard Litz Wire | Served Litz Wire | Selfbonding Litz Wire | Smartbond | |
---|---|---|---|---|
Stability of coil | - | good | medium | good |
Flexibility / windability | soft | more stiff | soft | soft |
Bonding process | - | solvent | hot air | hot air |
Mechanical protection | avg | good | avg | good |
Surface and haptic | - | rough | avg | smooth |
Second adhesion step without additional adhesion |
no | no | limited | yes |
Diameter of litz wire and copper fill factor
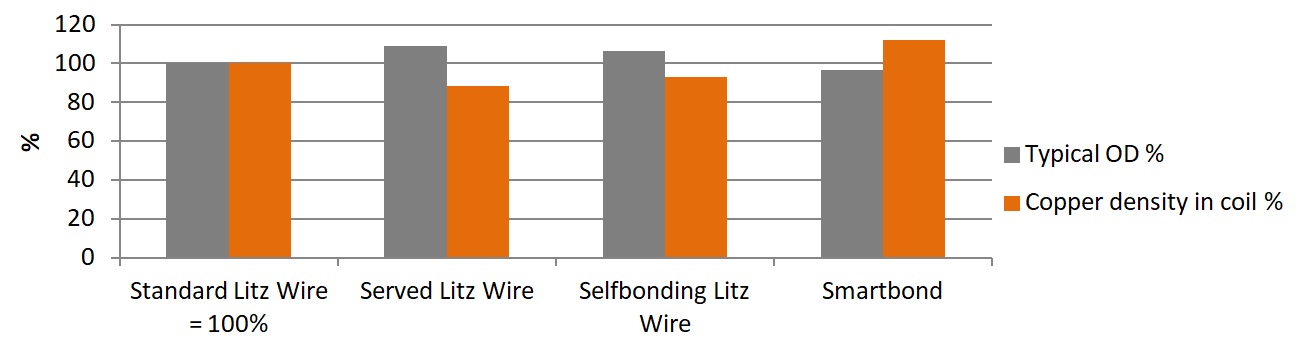
Dimensions
Diameter of single wires | 0.020 - 0.500 | mm |
Outer diameter of litz wires | 0.500 - 3.500 | mm |
Applications
- transmitter coil for wireless charging
- receiver coil for wireless charging
- wireless power charger
- coreless coils in different applications
LW Served
Served Litz Wire
General
High frequency litz wire served with natural silk, polyester, or nylon is characterized by increased dimensional stability and mechanical protection. The optimized serving tension ensures high flexibility and splicing- or spring up prevention during the process of cutting the litz wire. This splicing effect can cause handing and contacting of the wire ends more difficult in post processing.
Features and benefits of served litz wires
- Additional protection against mechanical stress
- Excellent dimensional and physical stability
- High flexibility
- Splicing prevention
- Good solderability above temperatures of 410 °C
- Improved impregnation
- Optimization of winding capacity
- Serving material allows optimization of insulation distances
Technical properties of served litz wires
Technical values of serving material
Serving materials1) | Silk | Nylon | Polyester* | |
---|---|---|---|---|
Thermal properties | ||||
Recommended permanent use temperature | 110 | 120 | 120 | °C |
Melting temperature | - | 250 - 260 | 250 - 260 | °C |
Elektrical properties | ||||
Dielektric constant ℇr | 1.4 | 3.4 | 3.2 | |
Mechanical properties | ||||
Elongation at break (dry) | 13 - 25 | 25 - 46 | 20 | % |
Moisture absorption (65% rel. humidity, 21°C) | 9 | 2.5 - 4 | 0.2 - 0.5 | % |
Other | ||||
Color | white, green | white | white | |
Dimensions
Serving materials1) | Silk | Nylon | Polyester* | |
---|---|---|---|---|
Diameter of single wires2) | 0.020 - 0.300 | 0.020 - 0.300 | 0.020 - 0.300 | mm |
Number of single wires3) | 2 - 25,000 | 2 - 25,000 | 2 - 25,000 | pcs |
outer diameter of litz wires | 0.071 - 4.0 | 0.071 - 10.0 | 0.071 - 4.0 | mm |
Number of layers (typ.) | 1 - 2 | 1 - 2 | 1 - 2 |
* Available in Asia only
1) customized solution on demand (thermo adhesive yarns)
2) other diameters on demand
3) depending on number of single wires
Applications
- HF transformers
- HF in-/converters
- HF transceivers
- HF chokes
- Inductive charger
LW With Strain Relief
Litz Wire with Strain Relief
General
Some of the ultrafine litz wires are impacted by high mechanical forces during further processing and over their lifetime. Litz wire constructions starting from an available single conductor diameter of 0.01 mm (AWG 58) can be designed implementing strain reliefs to improve the resistivity of the litz wire against tensile stress. It is typically used in applications where litz wire is used not wound in a coil, but used like a cable.
Features and benefits of litz wires with strain
- Excellent increase of tensile strength and flex life performance
- Different strain relief materials can be selected for individual applications
- Protection of super fine litz wires against mechanical stress
- Strain reliefs can be used in all other litz wire constructions
Properties of litz wires with strain relief
Comparison of properties with a typical litz wire
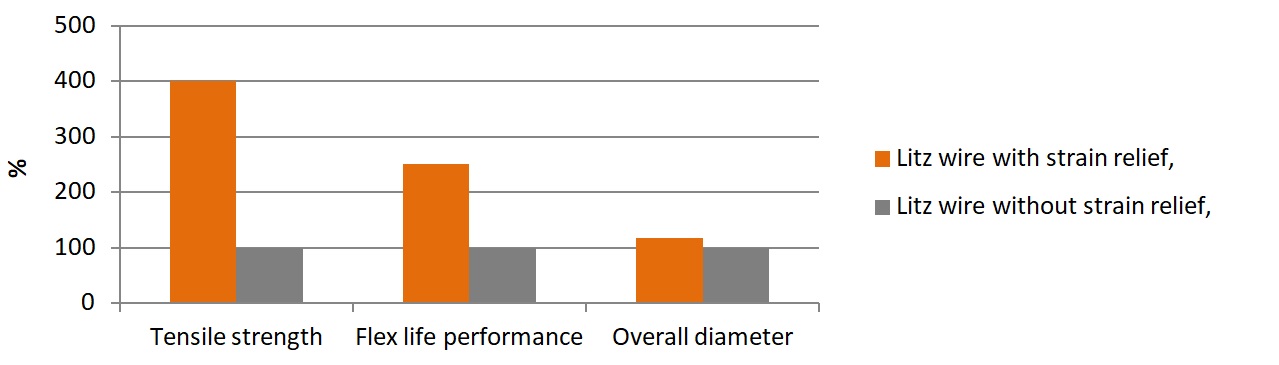
Technical values of strain relief materials
Materials | Polyester PES |
Polymer LCP |
Polyamide Aramide |
|
---|---|---|---|---|
from | ||||
Gram per 10,000 m | dtex | 30 | 110 | 110 |
Tensile strength | N | 1.5 | 29.6 | 26.7 |
Elongation | % | 9.8 | 3.3 | 3.9 |
to | ||||
Gram per 10,000 m | dtex | 450 | 440 | 420 |
Tensile strength | N | 29.4 | 99.2 | 49.7 |
Elongation | % | 12.4 | 3.4 | 4.2 |
Dimensions of litz wire with strain relief
Dimensions
Diameter of single wire | 0.020 - 0.500 | mm |
Number of single wires | 2 - 5,000 | pcs |
Outer diameter of litz wire | 0.020 - 2.5 | mm |